This report describes the development and use of a simulation framework that is meant to assist towards fabrication of an open TEM cell that fulfils the field uniformity criteria according to the IEC 61000-4-20 standard. The EUT (Equipment Under Test) should be placed on the bottom of the TEM cell and the field uniformity is to be assessed according to the standard. Because the optimal design of the TEM cell is unknown (choice of geometry dimensions, materials, connectors), there is need to streamline the simulation flow by parameterising these options, so that parametric sweeps could be performed, thereby enabling multiple geometry variations within one simulation.
The simulation framework relies on scripting and is able to automatise the process that starts with designing the dimensions of the TEM cell and ends with evaluation of the field uniformity test. A MATLAB API that generates VBScript code is used, meaning that the entire process of simulation and test evaluation is designed and controlled within MATLAB [1]. The resulting simulation flow allows to automatically generate the TEM cell geometry and set up a para- metric sweep where multiple dimensions can be varied, followed by automatic evaluation of the field uniformity test. Among the evaluated design variations, one that can fulfil the fieeld uniformity criteria can ultimately be selected and fabricated.
Considerations regarding the physics of TEM cells, the choice of design dimensions, and the implementation of the field uniformity test are not described in this report. The reader is encouraged to refer to the references for those considerations [2-12]. Therefore, this report begins with a section where the TEM cell geometry is designed in MATLAB and the HFSS sim- ulation is set up. Then, a section is dedicated to evaluating the field uniformity test, along with presenting and discussing the results.
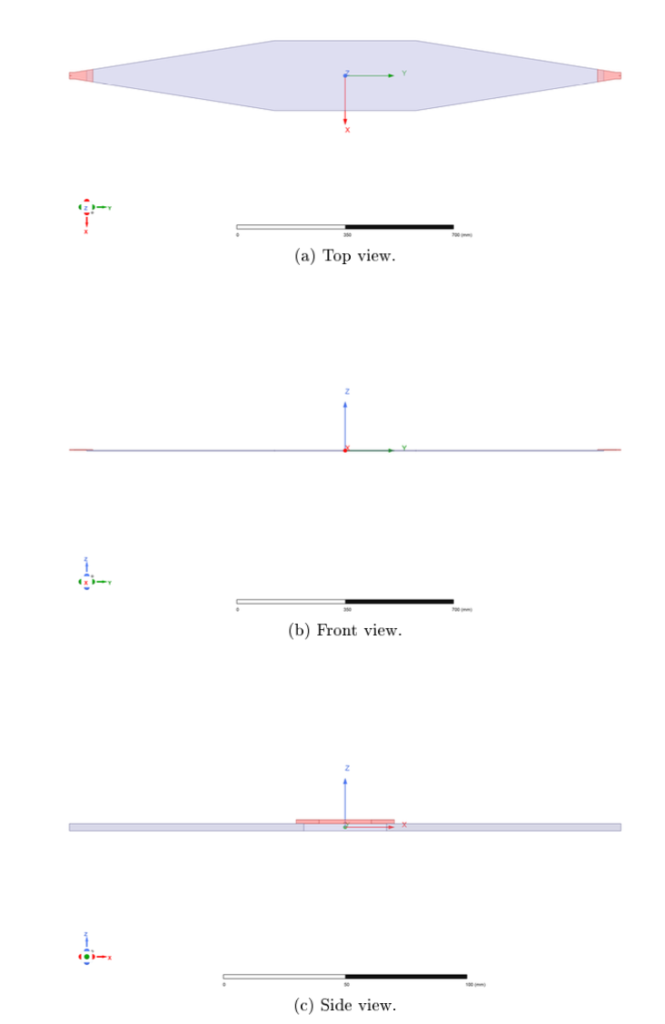
The user documentation can be downloaded here: . User documentation. The info about TEM Cell theory can be found in the following document.